Automation
with Electrical/Electronic Panel
The Control System with an Electrical/Electronic Panel is a customized control box for controlling existing conveyors.
Uptime Advantage
Compact design for mounting under the conveyor system with required I/O control.
Features
- PLC Based Logic Control
- MS Body with Powder coated.
- Electrical panel design as per Industrial Standards
- Bi-directional air cooling
- Multiple Input/Output controls
- Electrical panel design as per Industrial Standards
- Designed to withstand tough production line environments.
- Wall/floor mounting designed.
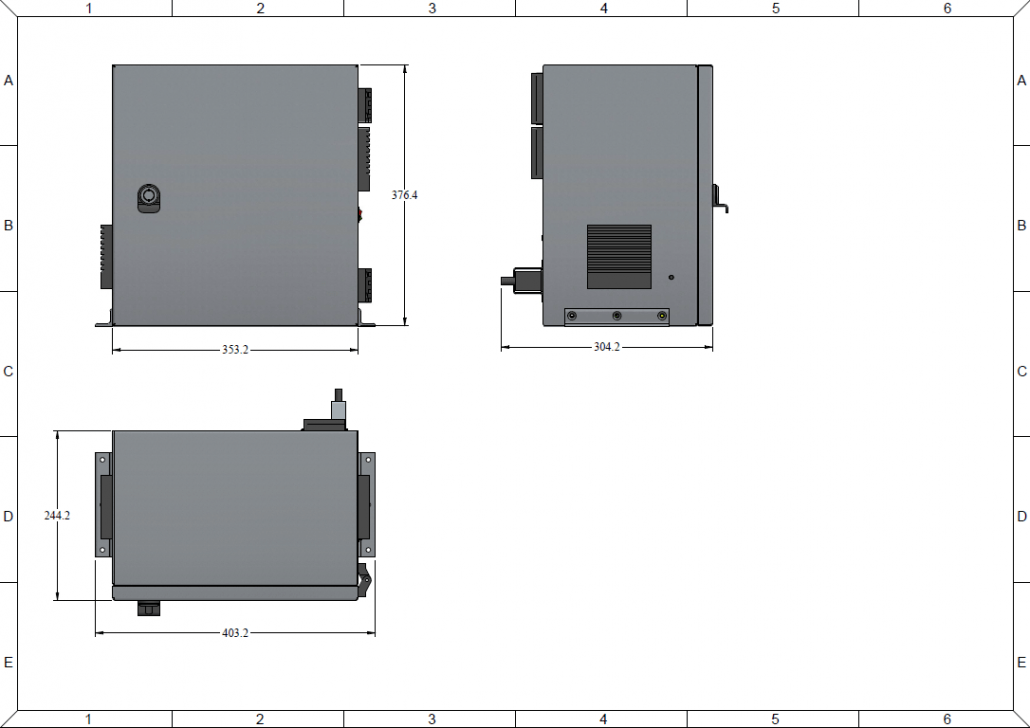
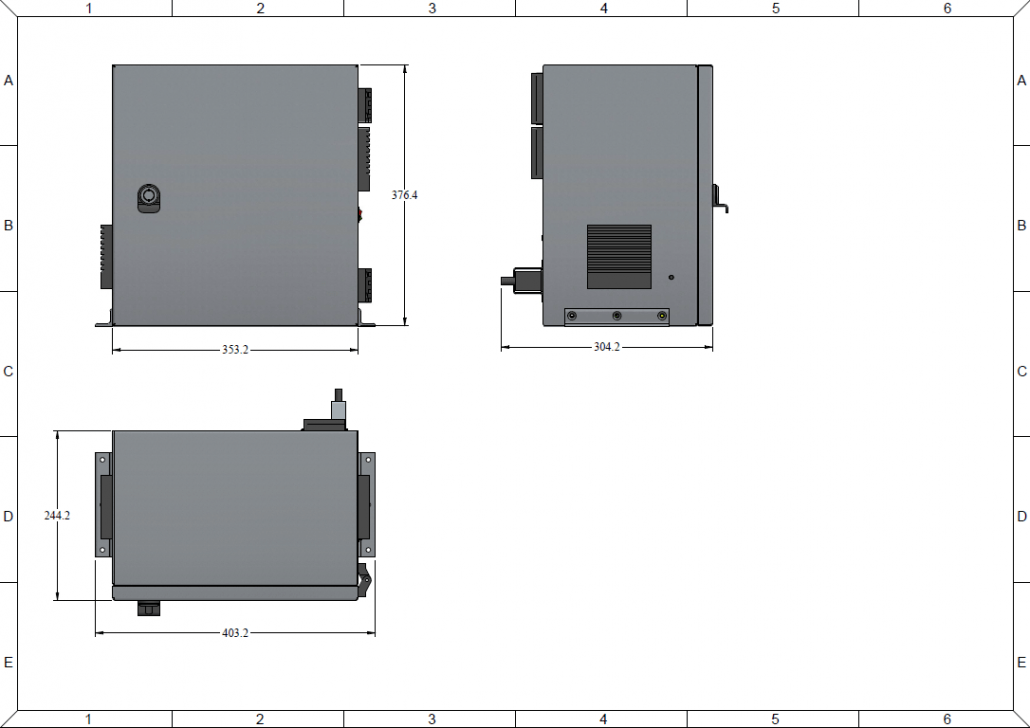
Parameter | description |
---|---|
Control System with Electrical/Electronic Panel | • PLC-based Controller • Electrical Standard wiringable high-resolution lens with minimum distortion is provided based on camera model. |
Embedded I/O controller with embedded software | • I/O Controller – Processing and controlling hardware signal and communicating with software; this controller integrates with sensor electrical/electronic parts. • I/O Communication |
Material of Construction | • Covers – SS304 |
External communications | • RS232, Ethernet, USB |
Operating temperature | • 5°-40°C |
Power supply | • 230 Volt AC, single phase with MCB for protection |
The Product Diverting Station is a customized system designed to scan 1D/2D code, divert it to different conveyors, and apply 2D code labels on pre-defined product boxes.
Features
- Plug & Play System
- User-friendly Operation Panel
- Auto triggering system
- User-friendly Operating Panel & intuitive Menu Navigation
- Customized Illumination for glossy surfaces
- Ergonomic design as per Industrial Standards
- Robust 1D / 2D code algorithm to decode multiple codes in a single scan.
- Variable Speed Belt Conveyor with adjustable Side guide rod.
- Multiple High-resolution cameras suitable for decoding even 8 x 8 mm 2D codes for larger scan area
- State-of-the-art reflection-free illumination ensures multiple 1D / 2D code decoding over glossy surfaces.
- Designed to withstand tough production line environments.
- Improving production line up-time
- Quick product changeover
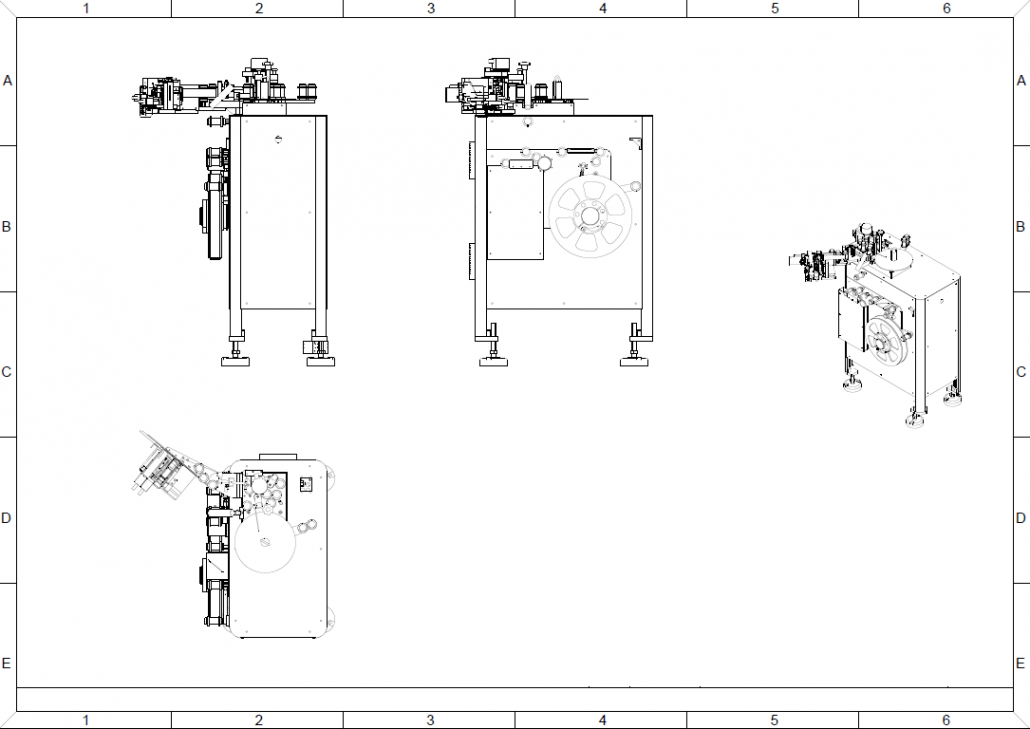
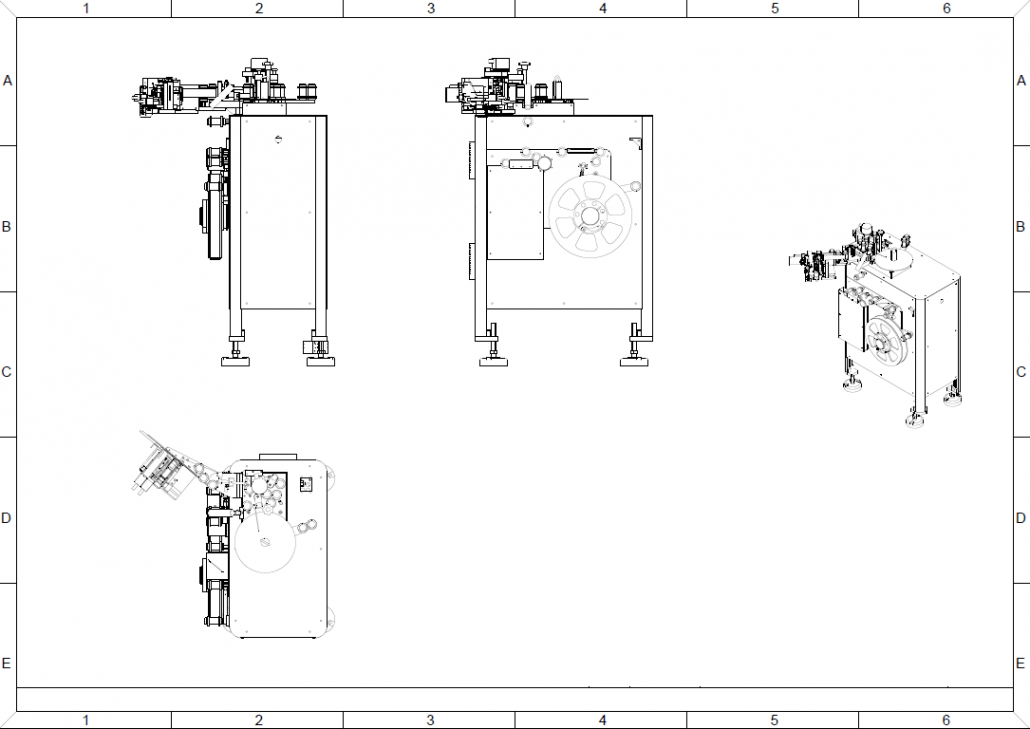
Parameter | description |
---|---|
Product Diverting Station | • Camera - High resolution camera for 1D/2D/QR code scanning • Lens – A suitable high-resolution lens with minimum distortion is provided based on camera model. • Illumination - White LED, reflection free homogeneous illumination for reflective surface (inside plastic scanning) • Simultaneous scanning of diverted products for verification • Sensors (as applicable) • Ejector - Pneumatic pusher with rejection bin • Print and apply to label unit camera to inspect label 1D/2D/QR code • Traffic management system for jamming bundles |
PC | • Processor Group - Intel Chipset High speed controller, above 2.2 GHz • Operating System – Windows 10 Pro • Memory Capacity - 4 GB • Storage Capacity - 120 GB SSD • Display Size – 15” or 17” • Operator interface – LED/LCD and touch screen |
Embedded I/O controller with embedded software | • Camera - High resolution camera for 1D/2D/QR code scanning • Lens – A suitable high-resolution lens with minimum distortion is provided based on the camera model. • Illumination - White LED, reflection-free homogeneous illumination for reflective surface (inside plastic scanning) • Simultaneous scanning of diverted products for verification • Sensors (as applicable) • Ejector - Pneumatic pusher with rejection bin • Print and apply to label unit camera to inspect label 1D/2D/QR code • Traffic management system for jamming bundles |
Material of Construction | • Section frame, Structure, Plates – Aluminium • Covers – SS304 |
External communications | • RS232, Ethernet, USB |
Operating temperature | • 5°-40°C |
Power supply | • 230 Volt AC, single phase with MCB for protection |
The Manual Scanning Machine is a customized scanning system mounted on an existing camera system, designed to scan pre-printed codes present on the box for verification and validation with the Database.
Uptime Advantage
Simple and Easy interface software for existing camera system, no intermediate or third-party software integration required.
Features
- Connect with Multiple Camera Systems
- PLC-based triggering system.
- User-friendly Operating Panel & intuitive Menu Navigation
- Quick product changeover
- Inbuilt Database facility for quick data processing
- Ergonomic design as per Industrial Standards
- Floor mounting stand for quick installation
- Designed to withstand tough production line environments.
- Improving production line up-time
- Interlock facility for existing conveyor system
- Wi-Fi handheld scanner for manual scanning option
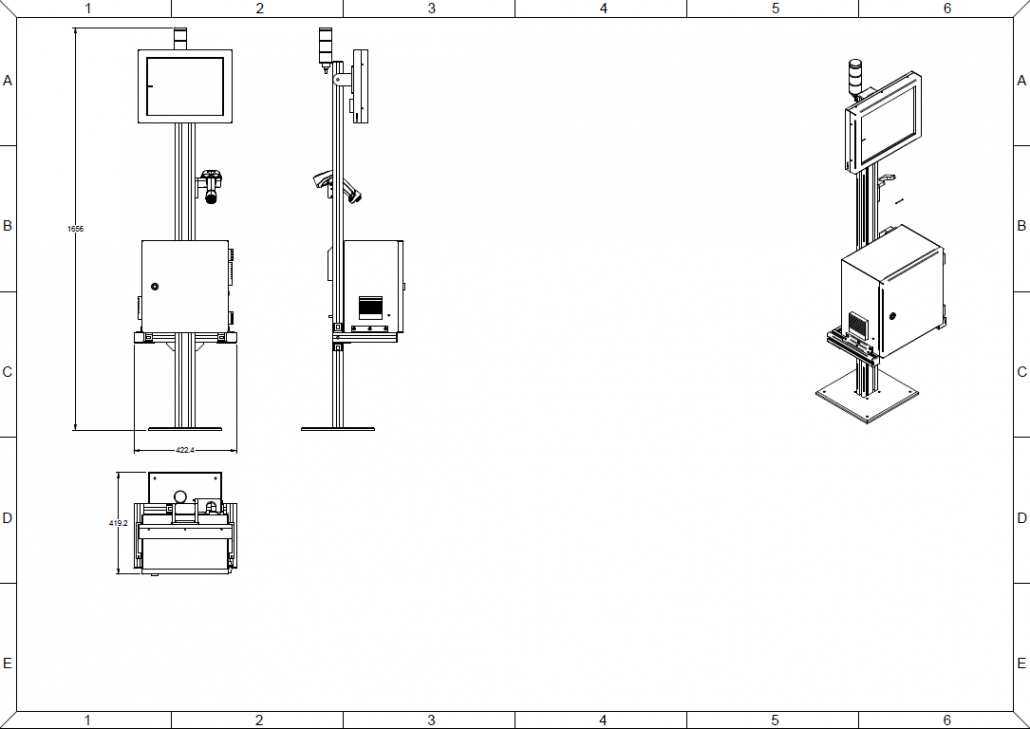
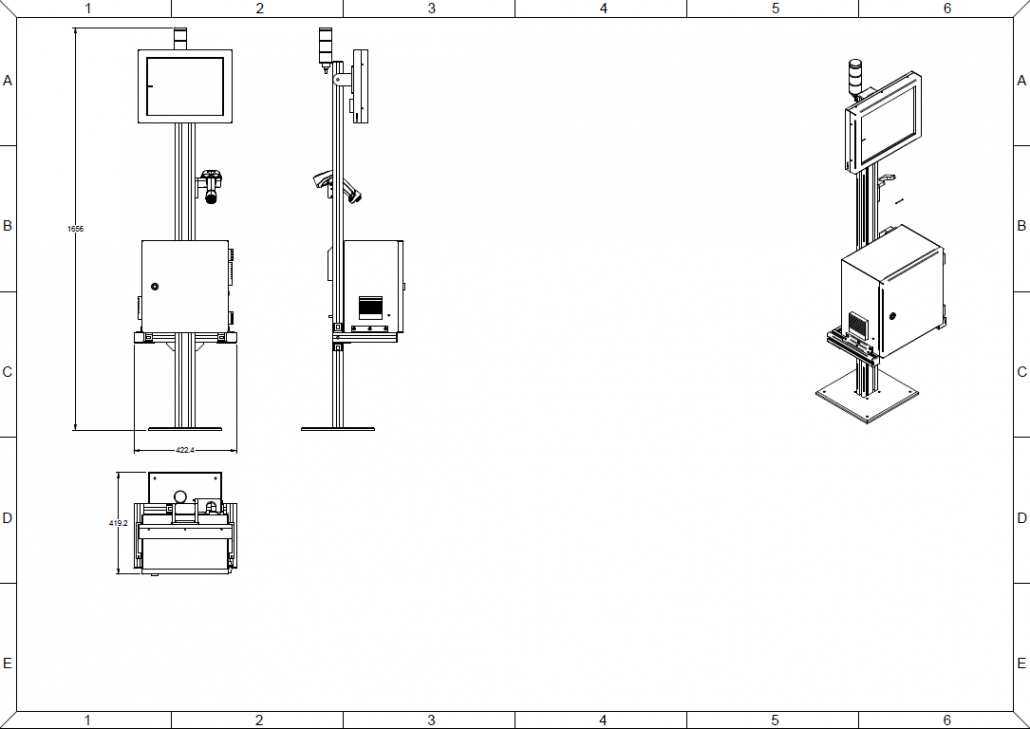
Parameter | description |
---|---|
Manual Scanning Machine | • I/O Controller – Processing and controlling hardware signal and communicating with software; this controller integrates with sensor electrical/electronic parts. • Camera communication • I/O Communication • Solid State Relay card • Required cables |
PC | • I/O Controller – Processing and controlling hardware signal and communicating with software; this controller integrates with sensor, electrical/electronic parts. • Camera communication • I/O Communication • Solid State Relay card • Required cables |
Embedded I/O controller with embedded software | • Processor Group - Intel Chipset High-speed controller, above 2.2 GHz • Operating System – Windows 10 Pro • Memory Capacity - 4 GB • Storage Capacity - 120 GB SSD • Display Size – 15” or 17” • Operator interface – LED/LCD and touch screen |
Material of Construction | • Section frame, Structure, Plates – Aluminium • Covers – SS304 |
External communications | • RS232, Ethernet, USB |
Operating temperature | • 5°-40°C |
Power supply | • 230 Volt AC, single phase with MCB for protection |
The Multi Scanning Machine is a customized scanning system designed to scan multiple pre-printed codes at the top of the box. It is available in two variants.
It is a top-side camera-based system with variable depth of field. As well as it's suitable for manual standing operations.
Uptime Advantage
No camera adjustment is required to scan codes at various heights.
Features
- Auto triggering system
- User-friendly Operating Panel & intuitive Menu Navigation
- Customized Illumination for glossy surfaces
- Ergonomic design as per Industrial Standards
- Robust 1D / 2D code algorithm to decode multiple codes in a single scan.
- Auto triggering along with manual trigger option.
- High-resolution camera (20 Megapixels) suitable for decoding even 8 x 8 mm 2D codes
- State-of-the-art reflection-free illumination ensures multiple 1D / 2D code decoding over glossy surfaces.
- Designed to withstand tough production line environments.
- Improving production line up-time
- Quick product changeover
- Adjustable guides for variable packing size to ensure the correct positioning of the product.
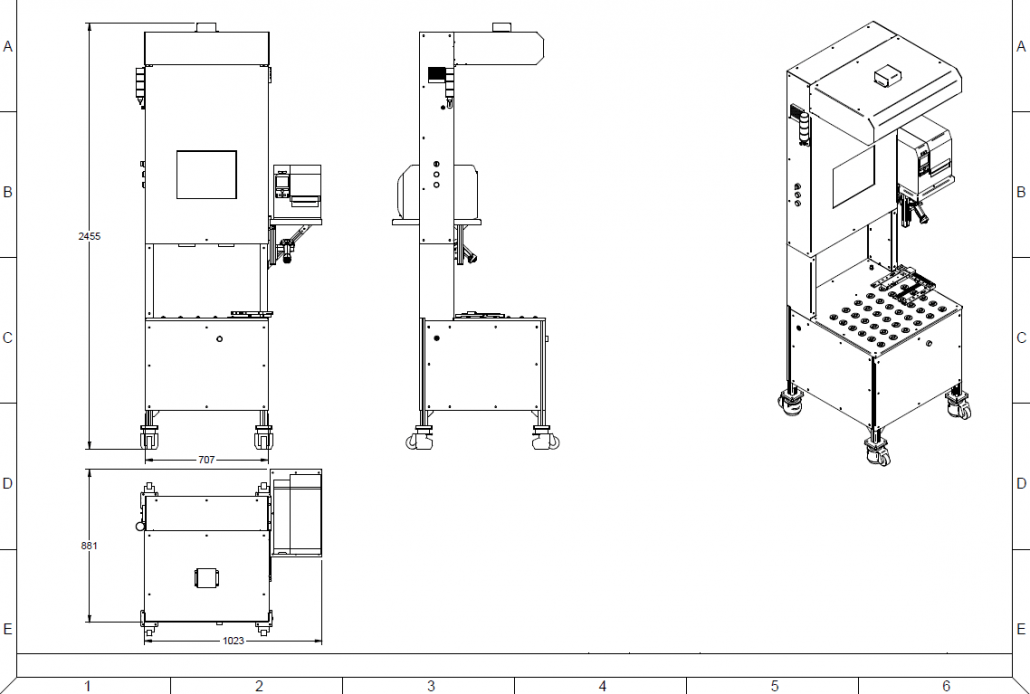
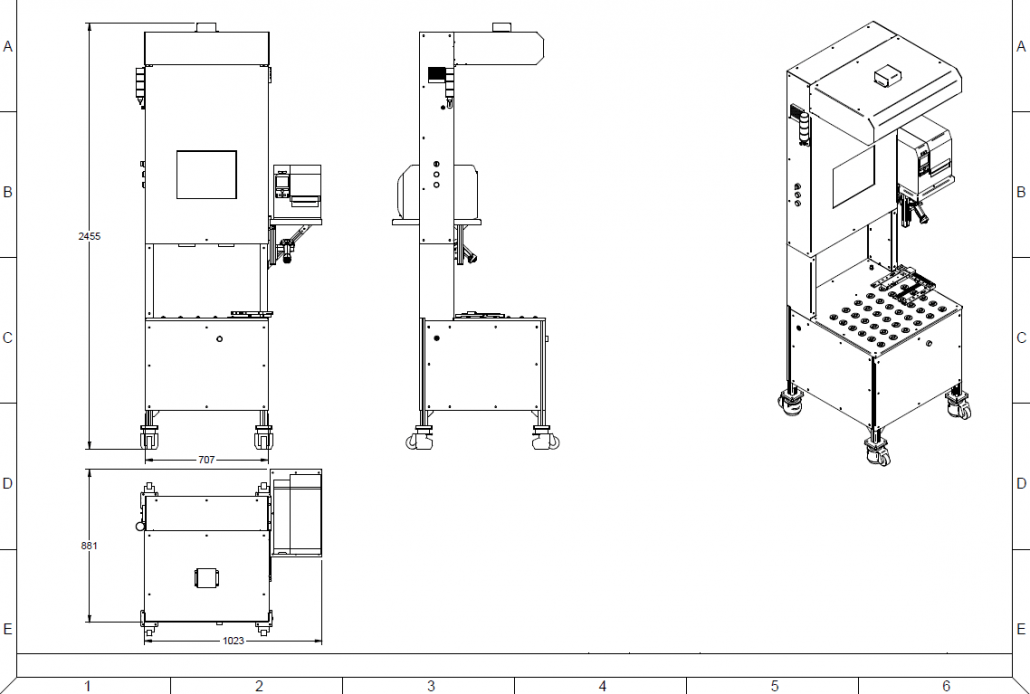
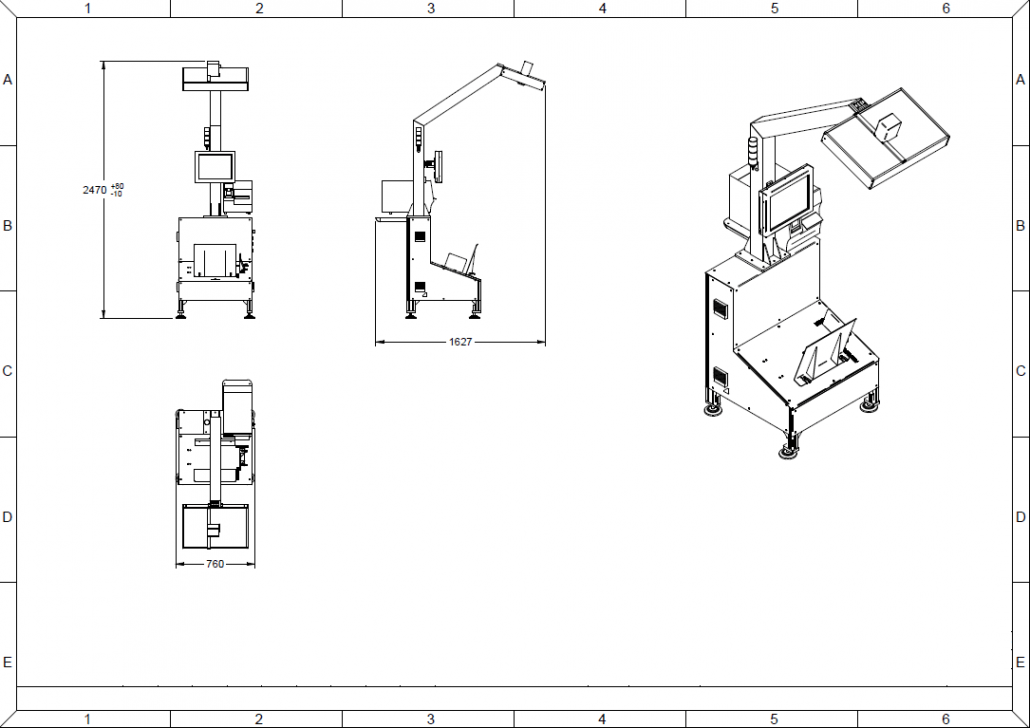
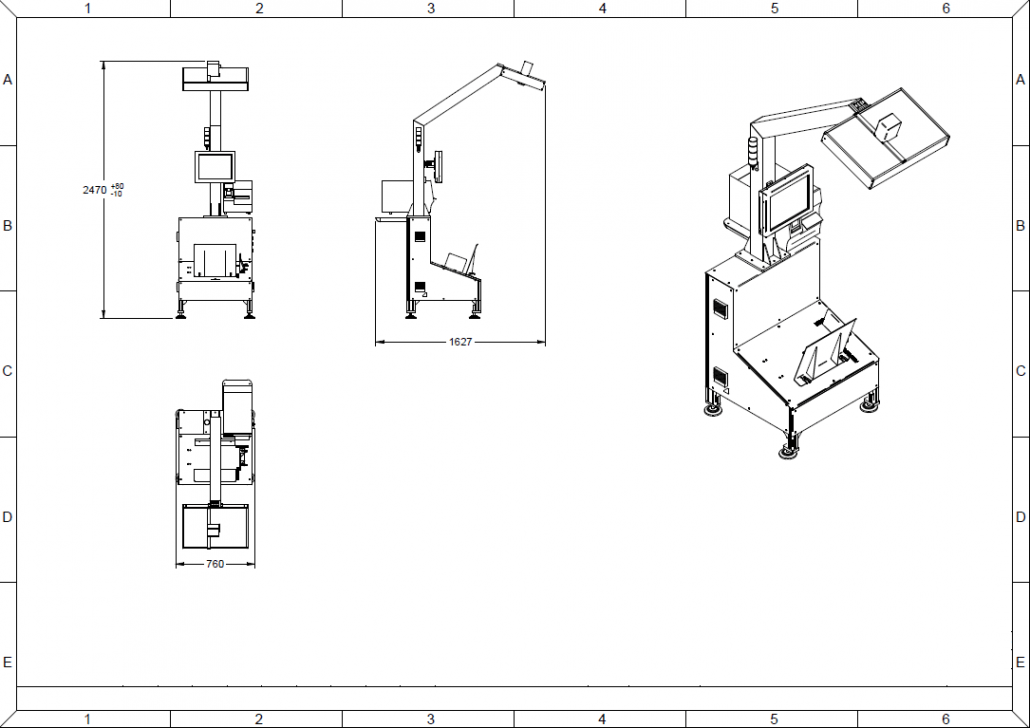
Parameter | description |
---|---|
Automatic Scanning Machine | • Operator interface – LED/LCD and touchscreen • Camera - High-resolution camera to scan or inspect the printed 2D Code. • Lens – A suitable high-resolution lens with minimum distortion is provided based on the camera model. • Illumination - White LED, reflection-free homogeneous illumination • Sensor - Limit Switch • Audible and visual alarm • Maximum Scanning Area (L x W x H) – 300mm X 200mm X 150mm |
PC | • Processor Group - Intel Chipset High-speed controller, above 2.2 GHz • Operating System – Windows 10 Pro • Memory Capacity - 4 GB • Storage Capacity - 120 GB SSD • Display Size – 15” or 17” |
Embedded I/O controller with embedded software | • I/O Controller – Processing and controlling hardware signal and communicating with software, this controller integrates with sensor, and electrical/electronic parts. • Camera communication • I/O Communication |
Material of Construction | • Section frame, Structure, Plates – Aluminium • Covers – SS304/MS |
External communications | • RS232, Ethernet, USB |
Operating temperature | • 5°-40°C |
Power supply | • 230 Volt AC, single phase with MCB for protection |
Automatic Scanning Machine
The Automatic Scanning Machine is specially designed for Online scanning of 1D/2D code present on the side of the box and in line with the Existing Conveyor System.
Designed to facilitate overall more productive operation with simple maintenance.
Features
- Plug & Play System
- User-friendly Operation Panel
- High-speed 1D/2D code Scanning Algorithm
- A vibration-free belt conveyor with a rejection bin. Polycarbonate enclosure.
- Traffic management maintains a gap between consecutive boxes, which reduces rejection and rework.
- Mirrorless multiple-resolution smart cameras with customized optics
- Robust 1D/2D code reading algorithm, which ensures minimum false rejection.
- State-of-the-art reflection-free illumination for more accurate shrink pack 1D/2D code decoding.
- Innovative design to accommodate the print and apply equipment within the machine.
- High-resolution camera to scan and verify the 2D Code on the box label.
- Integrated software can communicate with multiple cameras in the system.
- If the 1D/2D code is not scanned, the system does not apply the label on the Box. This avoids label wastage.
- Label roll changeover without stoppage of the production line.
- Various interlocks like rejection verification, rejection bin full, low air pressure, door open, etc.
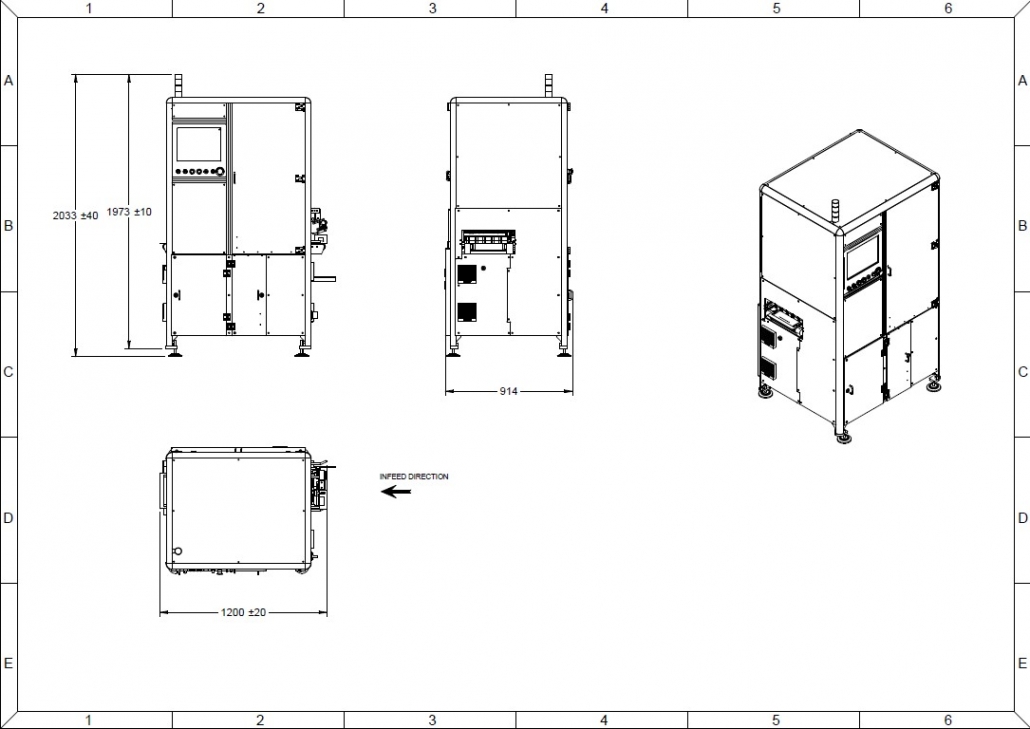
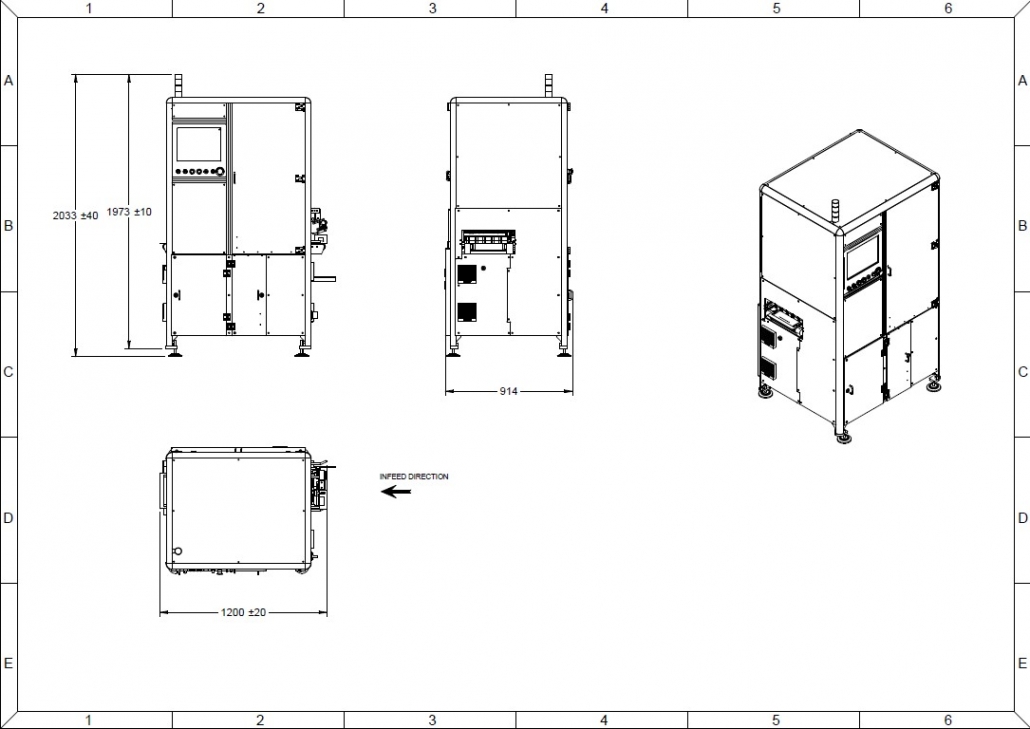
Parameter | description |
---|---|
Automatic Scanning Machine | • Camera - High resolution camera for box code scanning • Lens – Suitable high-resolution lens with minimum distortion is provided based on camera model. • Illumination - White LED, reflection free homogeneous illumination for reflective surface (inside plastic scanning) • Audible & Visual alarm • Sensors (as applicable) – Object, Target, Label detection, rejection verification sensor and rejection bin full sensor • Ejector -Pneumatic pusher with rejection bin • Conveyor with Traffic management to maintain gap and avoid jamming. • Print and apply labelling unit camera to inspect label 1D/2D /QR Code |
PC | • Processor Group - Intel Chipset High speed controller, above 2.2 GHz • Operating System – Windows 10 Pro • Memory Capacity - 4 GB • Storage Capacity - 120 GB SSD • Display Size – 15” or 17” • Operator interface – LED/LCD and touch screen |
Embedded I/O controller with embedded software | • I/O Controller – Processing & Controlling hardware signal and communicating with software, this controller integrates with sensor, electrical/electronic parts. • Camera communication • I/O Communication • Solid State Relay card • Required cables |
Material of Construction | • Section frame, Structure, Plates – Aluminium • Covers – SS304 |
External communications | • RS232, Ethernet, USB |
Operating temperature | • 5°-40°C |
Power supply | • 230 Volt AC, single phase with MCB for protection |
Products listed: Automatic Scanning Station 1 | Multi Scanning Station 2 | Manual Scanning Station 3 | Product Diverting Station | Control System